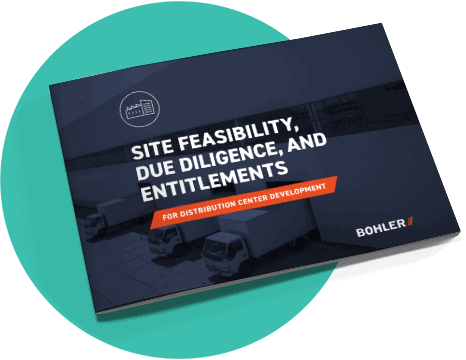
New to Distribution Center Development?
Fast forward your success with key market insights and answers to your most pressing questions.
Download NowThe Lehigh Valley Flex Center addresses the growing demand for light manufacturing and small-footprint industrial spaces (80,000–150,000 SF) in Lehigh Valley, PA.
Bohler provided site civil engineering and permitting services for this 31-acre redevelopment, transforming former office space into a 470,000 SF industrial complex with three buildings and parking for over 40 trailers.
Given the sinkhole-prone karst topography, Bohler designed a large, multilayer, above-ground infiltration basin instead of a series of underground basins as recommended by the Township. This design helped to spread water across a larger area, away from the buildings, parking, and driveway areas of the site, reducing the risk of concentrated infiltration that could trigger sinkholes under developed areas of the site. Existing stormwater pipes were rerouted, and off-site runoff through the site was carefully managed to further mitigate risks.
Bohler implemented phased construction sequencing, allowing individual units to become operational while adjacent phases were still under construction. Multiple site entrances on two road frontages supported seamless grading and site circulation. A detailed cut/fill analysis optimized soil movement, ensuring efficient use of on-site resources without disrupting completed phases.
The project team repurposed the existing parking lot by grinding the asphalt into 2A stone to serve as a subbase for new pavement. This sustainable approach reduced material costs while maintaining structural integrity with the approval of the geotechnical engineer.
Separate driveways were designed for employee vehicles and truck traffic, enhancing safety and operational efficiency. Main drives were strategically placed to handle the consistent flow of trucks, improving logistics for future tenants.
Bohler’s innovative stormwater design, precise grading solutions, and phased construction strategy allowed J.G. Petrucci to deliver operational space to the market faster. By overcoming complex site challenges and addressing regional demand for small industrial spaces, Bohler ensured a project that benefits both the developer and the local community.
Our approach makes a meaningful difference for our most ambitious clients. Contact us to learn more.
Let's Get Started